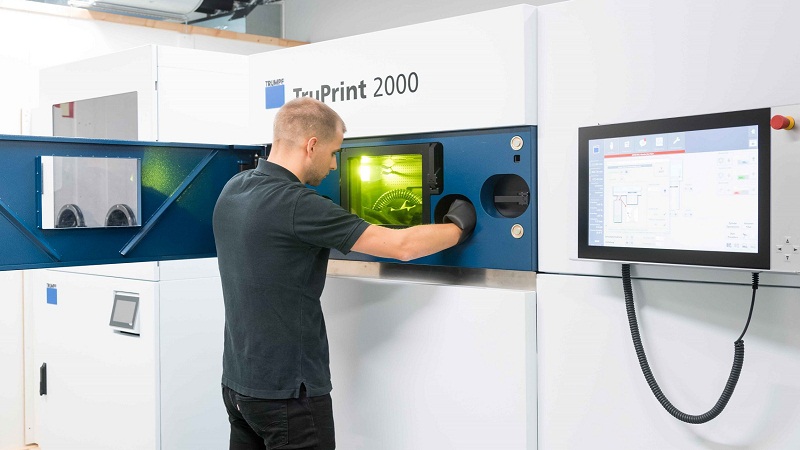
TRUMPF, a German High-Tech Company launched a new 3D Printer- TruPrint 2000, at Frankfurt’s Formnext 2019, which is believed to be compatible with environment of aerospace, automotive, mechanical engineering, tool and mold making, as well as the medical and dental engineering industries. The machine processes the printing powder in an inert gas environment, which prevents contaminants from infiltrating the powder circuit and is a key advantage for applications such as sensitive medical devices. The TruPrint 2000 features a multilaser design with two 300-watt lasers working in tandem and is capable of printing parts out of Titanium. Additionally, the machine includes automated powder bed and melts pool quality monitoring, notification in the event of an error, and an end-to-end documentation trail.