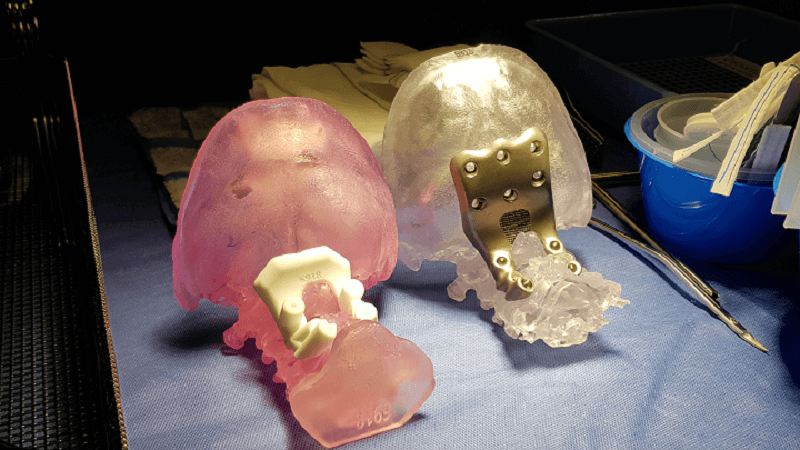
Paul D’urso, MD, Anatomics Founder and a neurosurgeon at Epworth Healthcare, had reported 700 spinal fusion procedures at the recent 3DHEALS conference in San Francisco. They also developed Atlantoaxial transarticular screw fixation, an effective technique for arthrodesis and discussed how biomodelling and 3D printing are both useful tools for pre-surgical planning, developing titanium implants and patient-specific tools, and intraoperative stereotaxy – a minimally invasive surgical procedure which uses a 3D coordinate system to locate small targets inside the body and then perform an action, like an ablation, biopsy, injection, or implantation.