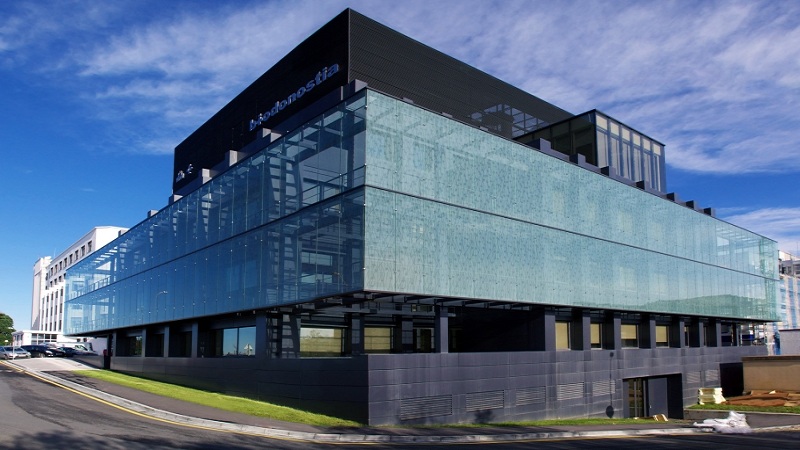
Biodonostia Health Research Institute, a medical research institute in Basque, Spain, recently partnered with Tecnun, a specialist division of the Universidad de Navarra, and Tknika, a regional Research and Applied Innovation Center for Vocational Education and training, in order to help its surgeons harness FDM 3D printing technology from Stratasys to help in surgical preparation and planning. With the help from partnership, the surgical teams can receive highly accurate 3D printed medical models, made with Stratasys’ FDM technology, within 24 hours which can help patient care by reducing the amount of time patients spend in surgery, especially surgeries for complex thoracic wall tumors.