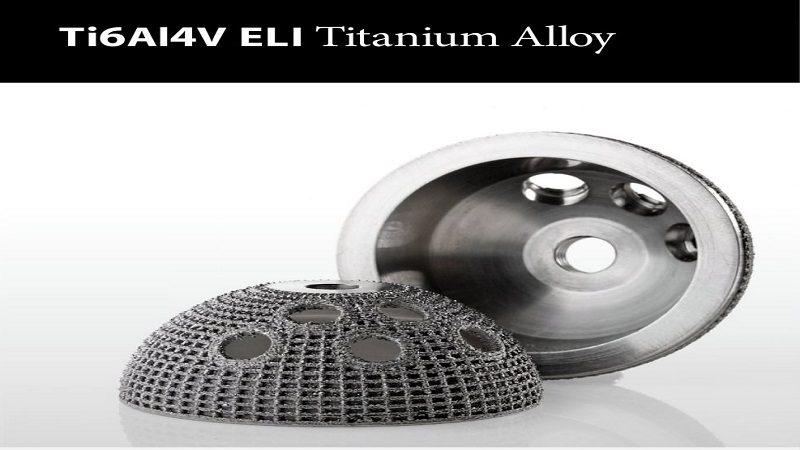
Ti6Al4V, a biomedical implant, is a titanium alloy with biocompatibility, mechanical properties, and excellent corrosion resistance but poor wear resistance, corrosion and stability. The researchers from Jiangsu University used Laser Peening (LP), a laser surface modification technology, to modify Ti6Al4V and the results concluded that the surface micro-hardness value of the LP-treated Ti6Al4V sample increased by 25.7%, showing that LP was able to strengthen its surface. Additionally, the results of the experiment showed that after being treated with LP, the specimen did have better wear resistance than the untreated one; laser energy and impact time also helped improve the wear resistance of the LP specimen.